It was anticipated that others would have offered alternatives or assistance by now. Hoping you have resolved the problem, I am still thinking about it. Even if you have completed your project please read on.
If you have found a solution that is absolutely great, it would be really useful if you would share it here.
Otherwise, do you have any information regarding the Sketch of the âformed sheet Aluminium componentâ?
During creation a Sketch has to be made on one of the three standard Panes:
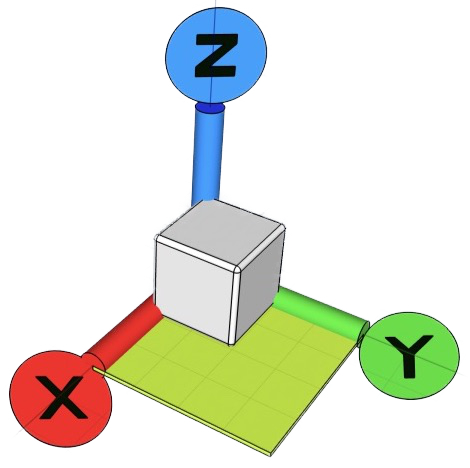
XY; YZ; ZX:
or perhaps a Construction Plane(s) [CP or CPs]?
Do you have any information about the âRed Faceâ lane regarding the set up of angles in relationship to any of the three standard Planes?
Such information may be useful to temporarily return the Red Face Plane to align with the Plane used to create the Imported Third party Pneumatic Cylinder? Importing the Cylinder and Snapping the two Items together should be straight forward. Except if it has been created an a skewed CP.
Alternatively, as previously suggested, double tap your Finger on the Red Face to provide a Plane on which to Sketch. Input your Component details or replicate the essential Lines in Sketches within the file below and then extrude appropriately.
This version of the Cylinder appears to be somewhat like the component you are using:
The details of this were taken from the internet providing dimensions to 0.01mm.
Educated guesses have been made regarding the Internal Details, Shaft Coupling, Piston and Cylinder Diameters. The information shows the âShaft/Piston/Cylinderâ Assembly as being 1mm higher than the centre line of the Body, I have placed it dead centre. The Rear End has not been properly completed, my guess is that the Cylinder has a âclosed-blankâ end?
The rear view showing the the Cylinder is the same as the front [Cylinder portion] with just a âfillerâ piece added.
The basic Body dimensions are 130.65 high x 121.85 wide x 171mm long, with Fixing Centres 94 x 94mm.
It remains a âwork in progressâ subject to any âadjustmentsâ being needed.
If you can provide the dimensions, interested only in finding a resolution, I will be happy to produce a Cylinder to the exact dimensions, of your Component. If you do not NEED to do this I would still welcome the opportunity to complete this project as it will be at least one more method tried and either accepted or rejected.
You would also need to supply an Uploaded Copy of your Design MINUS ALL detail, except a CP formed by placing it directly on the Red Face [i.e., Zero Offset]. However some means of accurately positioning the Cylinder on that CP would be required, e.g., Mounting Hole Locations.
Either Cylinder, i.e., yours or the one on this page mounted on the virtually empty new CP Design would be completed and Uploaded, by me, so that you could transfer it to your copy/duplicate copy of your full Design.
Excluding the Location Point(s) the only aspects that will be visible publicly are the CP and the details of the Pneumatic Cylinder, the latter probably being commercially available anyway.
I have other commitments for the next two days but hopefully an outcome would become available during the weekend.
Here is the File:
Pneumatic Cylinder.shapr (496 KB)